- Nicolas Vaillancourt
- Oct 29, 2019
- 4 min read
Updated: Nov 3, 2019
By using 3D printed parts, we have been able to develop and improve mechanism on our device quickly and efficiently.

Over the past month, our team has gone through a lot of ideas and tests in order to improve our chances of high performance at the competition. In going through many ideas and iterations, we have made a lot of progress on our working design.
Our design process has been very effective: we start by brainstorming an idea to improve our project. Next we make a prototype to test the viability of our idea, and finally we manufacture the working versions of this idea that will be implemented into our design.
Since manufacturing the working design is usually the hardest part, we have been lucky to have access to a 3D printer at my house and benefited from the use of CAD. Because of the ability of 3D printers to quickly design a prototype or even a final part, we have been able to try many different ideas. This has led to the implementation of only the most practical solutions in our mechanisms.
One part of our project that has particularly benefited from our 3D designs has been the dropper/bounce mechanism. In it, the ping pong ball falls out of the transportation tubing into a funnel that leads into a 3D printed dropper and bounces off a 1.5 inch diameter piece of bar stock aluminum.
In this part of our project, there are many uses of 3D printed parts. One example is aluminum bar stock. This part is friction-mounted into an adapter piece, which holds it at 22.5 degrees off vertical when mounted to the platform. Manufacturing a mount that stable with an accurate angle would be a challenge without a 3D printer and would definitely take longer than the 70 minute print time.
Also, the funnel adapter and dropper would been a challenge to construct with it's accuracy in the hole diameter and 2 mounts to other systems, but designing and printing it from CAD was a simple exercise that allowed for lots of flexibility in the shape because of a lack of manufacturing constraints.
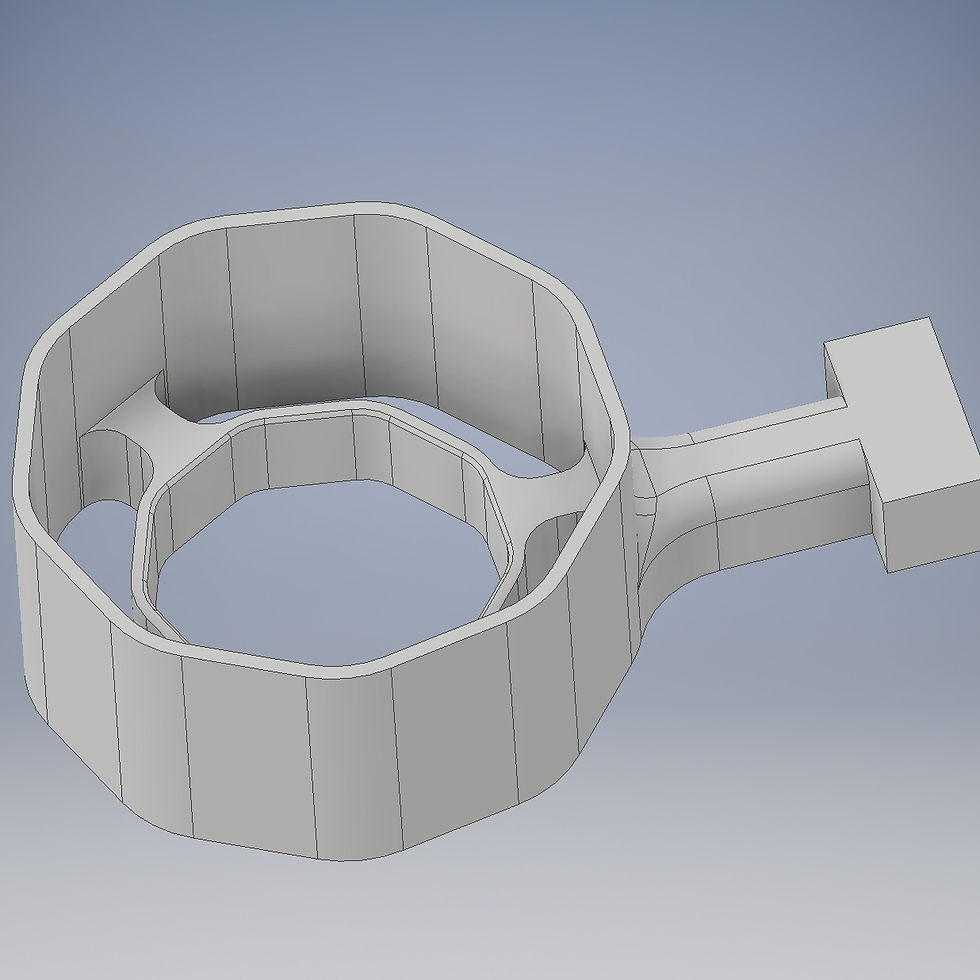
Although 3D printing has been a huge help in the design process, it has also come with some downsides. Because of some imperfections in the printer, each iteration of the dropper had to have its dropping hole sanded out to remove the ridges left from the layers of the printing filament. Another problem with 3D printing is shrinkage. 3D parts can change shape when on the heated bead and come out slightly warped. Also there is a concern that these parts may change shape over time when exposed to heat. This has not been a big problem for us except in the case of balls getting stuck in our 3D printed dropper because of a slightly ovular hole. This problem has been addressed with the new nonagon dropper but posed a problem for the weeks before.
In the upcoming weeks, our team is going to focus on refining our design. Also, we may need to send some questions to the JPL event coordinator about the potential dangers of using lasers for aiming of our device. In refining our device, we are going to work on ways we can increase the reliability of our mechanisms, building walls to block cross winds at the area of bouncing, making a platform and improving our loading mechanism, and working on improving the stability of our bouncing mechanism.
Some of the projects I have been working on my own are concepts for the mechanism of my robotics team. I also have been working on coding our robot to have a high level of control and maneuverability.
________________________
The only problem with this section of the design is that the ball will occasionally get stuck in the dropper. This is because of small imperfections in the spherical shape of the ball and a slightly oval hole in the 3D print. When the ball and the hole align in the wrong way, the ball will not drop. This problem is infrequent about 1 in 50 but if it occurred during a competition, it would end our run.
Our plan to fix this problem is lightly sanding the hole. The downside of fixing this problem is that the more we open the hole, the more accurate our device becomes and may become a problem that requires a redesign of our dropping mechanism.
I suspect that the biggest problem we will have to address in the coming weeks is the loading mechanism. Since the balls must be transported one at a time, we will have to make sure that only one can enter our device at once while not having a person directly touch the balls. We have a plan for how to drop one at a time consistently but there is another problem with airflow. Since the fan will be active during the entire run, there may be a problem with back pressure blocking balls from entering the tube. Depending on the internal resistance of the pipe and its turns, sometimes the fan will release pressure out of the hole where the balls enter or where they get in front of the fan.
I have recently been working on the JPL project outside of school and testing the way a ping pong ball bounces on different materials and shapes. I initially thought that using a ping pong paddle would be a good material to bounce off of but after some testing it became clear that there are much better materials to use. I found that the best material to use would be one that elastically collides with the ball.
To be as close to an elastic collision as possible, the material would have to be very stiff and have enough mass as not to rely on its mounting system. My first thought for the best material was metal. My tests found that aluminum and steel produced highly elastic bounces with only a slightly better performance with steel and they both would work as long as they were thick and heavy enough. I do not have access to much materials and could not find a suitable piece of metal at a hardware store so I decided that some scrap aluminum bar stock would be a good bouncing surface to use.
Kommentare